新能源汽车如何延长续驶里程一直备受行业关注。其中,车辆自重便是重要影响因素。
4月8-9日,由中国汽车材料网主办的“2021年(第六届)新能源汽车轻量化技术研讨会暨展示会”在苏州召开。本届研讨会吸引了来自整车企业、零部件供应商及科研院所的专业人士参加,从结构优化设计、轻质材料应用、先进成型工艺三方面阐述了新能源汽车轻量化的途径,讨论了其未来发展方向。
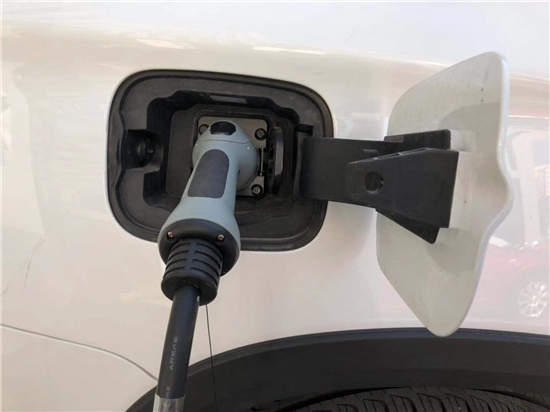
助推性能升级、产业转型
业内专家指出,新能源汽车轻量化技术的应用不仅能降低整车能耗,而且影响未来汽车的设计理念,成为汽车技术革命的主要推力。
中国汽车轻量化技术创新战略联盟研究员罗岩对《中国汽车报》记者表示,轻量化的意义不仅是节能减排,而且成为提升我国汽车产品竞争力的重要途径。“轻量化将影响车辆的加速性能、制动性能、操纵稳定性、平顺性和噪声振动水平。合理的结构设计和轻量化材料的应用将有效提升车辆的各项性能,科学合理的用材策略也有助于控制车辆的生产成本。”他说。
此前,中国汽车工程学会发布了《节能与新能源汽车技术路线图2.0》(以下简称《路线图2.0》)。《路线图2.0》提出,到2035年,传统能源动力乘用车将全部转变为混合动力,而新能源汽车将成为主流,销量占比达到50%以上,其中纯电动汽车将占比95%以上。
据了解,对于电动汽车来说,整车减重更是对提升续驶里程有着非常明显的作用。数据显示,在动力电池重量不变的前提下,如果实现能量回收,每减重100kg,A级车可增加续驶里程12.3km,C级车可增加续驶里程13.0km;整车整备质量不变,动力电池以外的部件每减重10kg并将降低的重量分给动力电池,A级车可增加续驶里程12.5km,C级车可增加续驶里程9.3km。
事实上,轻量化也是带动汽车产业链上下游相关领域转型升级的源动力。罗岩认为,汽车轻量化涉及冶金、化工、材料、装备、设计、维修、回收再利用等多个相关产业,过去10余年来对钢铁工业的带动作用已经显现。未来,轻量化将向产品多材料混合应用和生产智能化方向发展,将催生对汽车用材和生产装备的更高要求。
围绕三个“抓手”下功夫
来自东南(福建)汽车工业有限公司的参会代表江金寿表示,基于成本考量,轻量化的工作需要通过运用先进的结构设计方法,实现“恰当技术恰当用”,即合适的材料用于合适的地方。
中汽研(天津)汽车工程研究院有限公司高级专家吴昊对记者表示,在汽车设计开发阶段,通常采用CAE辅助分析方法对具体部位的零件形状及材料种类应用进行分析与确定。作为基础数据,材料的相关力学性能输入CAE仿真模型中进行结构性能分析计算,精准的材料模型与数据输入会使结构设计余量变得更加合理,从而使轻量化与整车性能更加完美地匹配。相反,如果材料模型与数据输入精度不高,将导致前期结构设计偏软或偏硬,进而对材料的精准应用产生影响,导致结构设计余量不足或过多,不能精准实现将合适材料应用在合适位置的设计理念。在车身结构设计阶段,材料与部件的精准仿真技术格外重要。
材料的应用是汽车轻量化最基础、最核心的手段,既能保证车体结构的性能,又可大幅度降低车体重量的材料。目前,行业内实现汽车轻量化,普遍使用的是高强度钢、碳纤维、铝合金、镁合金、工程塑料等材料。
一汽-大众汽车有限公司工艺开发工程师吴雪松介绍称,在镁合金、碳纤维等轻质材料的成本下降到能大规模应用水平之前,铝合金仍将是车身材料轻量化的最有效途径之一。铝材在轻量化中发挥着巨大的作用,但仍面临着成本、安全、性能及生产工艺等方面的多重挑战。
碳纤维材料也受到了不少与会代表的关注。数据显示,2020年,中国汽车交通领域的碳纤维需求占比达到1.8%。碳纤维复合材料是重要的汽车轻量化材料且非常具有市场潜力,吉林省华阳新材料研发有限公司工艺工程师宫元表示,华阳在行李箱护板、电池托架、板簧等方面都有应用碳纤维材料的案例,并在复合材料方面拥有成熟的产品设计流程和批量生产工艺。
“各种轻质材料都有其用武之地,汽车轻量化的发展将更加聚焦于优化设计和多材料混合应用。”罗岩表示,随着产品设计、成型和连接技术更加成熟,汽车轻量化市场将出现多种技术和多种技术路线并存的格局,“恰当”是未来企业在选择轻量化实现路径时的核心要求。比如,车辆不同部位减重的价值和可接受成本不同,其中车辆上部和前端部件的减重意义更加重大,可接受的轻量化额外成本也相对较高。整车企业在确定所采用的轻量化技术路线时,应更加注重对车辆市场定位、用户需求、性能与成本、产品效益和供应链体系的能力等因素的综合考量。
连接技术值得更多关注
多材料混合应用带来了新材料连接技术需求,铆接、粘接和复合连接等多种连接方式在汽车行业得到了快速的发展。因此,解决异种材料连接过程中的结构设计、接头力学模型、服役性能评价、工艺质量控制等一系列产业化的问题迫在眉睫。
对此,罗岩坦言,我国各种新型连接技术的研发工作都在推进,但现有成果与产业化应用仍有一定距离。与国外先进水平相比,国内企业连接结构的技术基础理论没有形成,设计规范没有建立,所需的(系列化、标准化、通用化)基本单元(如铆钉)缺失,连接工艺方法与装备的参数控制以及生产过程的质量控制等方面,都因实践不足而经验积累甚微,高性能连接密封材料和摩擦稳定剂等产品基本依赖从国外进口。
“随着轻量化需求越来越迫切,铝在乘用车中的应用将逐年增加,连接工艺和成型工艺的逐渐成熟将促进铝材的推广应用。”江金寿说。
吴昊表示,多种材料在车身上混合应用使得整车轻量化水平不断提高,为了适应不同材料之间的连接,SPR(自冲铆接)、FDS(热融紧固)、粘接等连接方式在车身上得到了大范围应用。这也对传统以焊接为主的连接测试与仿真方案提出了挑战,需要多材料混合车身连接方式的精准仿真。钢铝混合电阻点焊为钢铝连接提供了新的解决方案,电阻点焊工艺简单成本低,所需设备、人员和供应链均成熟。直接用于铝薄板及铝-钢异种材料焊接,可以节省大量投资及人力成本,简化工艺流程,有着一定的技术优势,通过工艺开发与性能研究,精准预测钢铝等材料的力学及疲劳性能。
郑重声明:本文版权归原作者所有,转载文章仅为传播更多信息之目的,如作者信息标记有误,请第一时间联系我们修改或删除,多谢。